CONVENTIONAL MINING AND MILLING OF URANIUM ORE
Introduction
Production of uranium concentrates, in the form of U3O8, or “Yellowcake” as it is commonly referred to in the industry, from ore which is mined by open pit or underground methods and processed to recover uranium, employs technology and methods common to the mining industry.
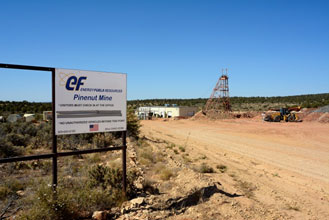
Throughout the 60+ year history of uranium mining in the U.S., the majority of uranium ore mined has been via conventional open pit or underground methods. The uranium “boom” period of the late 1970’s and early 1980’s witnessed considerable growth of the uranium mining industry in the United States, including development of large open pit, underground, and in-situ recovery operations. Many mining and milling production centers remained in operation through the middle 1980’s, however, continuing price erosion ultimately led to closure of many facilities.
Today there are no open pit uranium mining operations active in the U.S. Several underground mines have been reactivated in recent years, and a number of development projects are underway to prepare for resumption of past mining operations or development of new resources. This review focuses on underground mining of uranium as this method is currently experiencing renewed attention. Although open pit mining may also resume in the future, there are no large open pit projects under development at present in the U.S.
This review also provides an overview of the technology and the regulatory regime specific to uranium ore processing.
Underground Mining
Underground mining of uranium evolved from small scale operations in the rugged and remote rimrock and canyon land country of the Colorado Plateau region of southeastern Utah and southwestern Colorado. Before uranium mining started, vanadium deposits were mined in this region for decades. Uranium mining later took place at many of these same deposits, which contain both vanadium and uranium mineralization. The growth of the uranium industry in the 1960’s and 1970’s resulted in larger scale underground mining operations, and mines were opened across the West in Colorado, Utah, New Mexico, Arizona, Wyoming, Washington, and South Dakota.
The majority of the commercially viable uranium deposits in the U.S. occur in sandstone host rocks. In the early days of underground uranium mining, much of the sandstone rock was broken by hand and transported via small rail cars to the surface for stockpiling and shipment to an ore processing mill. As mining operations and production volumes increased, the use of rubber-tired diesel equipment supplanted rail mounted equipment.
Underground uranium mining requires the same basic sequence of development steps as required for any other type of underground mining. The ore deposits must be accessed, the mineralized material must be “developed” by constructing workings to provide access to the ore, the ore must be extracted (usually through drilling small diameters holes and blasting the ore), the broken ore must be transported to the surface, and finally the ore must be sent to an ore processing mill to extract the contained metals. Aside from designing and developing a mining operation specifically suited to the physical properties of the ore, underground uranium mining is not unique within the industry.
Early uranium miners often located mineralization on surface exposures, and followed the ore underground wherever it led. As mining practices evolved and production requirements increased, mining techniques improved and productivity increased greatly. Uranium deposits nowadays are typically outlined by drilling from the surface. Access into ore deposits is through vertical shafts or inclined openings (called “drifts” or “declines”). In the U.S., shaft mines typically range from a few hundred feet deep to more than 3,000 feet deep. Mines using declines for access are impractical for pursuing deep deposits, as the declines must be at a gradient that can be traversed by mining equipment, and increased depth equates to increased decline length.
In sandstone uranium mining, the ore is typically extracted using a “room and pillar” method where pillars of unbroken rock are left in place to support adjoining openings where ore is removed. Mine working are also supported by insertion of steel bolts into overlying strata to stabilize the ground, and in high traffic areas, mine openings are often lined with concrete, steel frames, or wood to ensure long term stability.
Each mining region is unique, and underground conditions are variable. The presence or absence of ground water, the quantity of ground water, the strength of the ore and surrounding rock, the geometry and orientation of mineral bodies, etc. all must be considered in mine design. When accessing ore bodies through shafts or declines, the surface “footprint” of underground uranium mines is small. Typical surface installations include offices, warehouse, maintenance and repair shops, power facilities, air compressor stations, pumping facilities if required, and stockpile areas. Waste rock from the initial development of a mine is deposited on the surface. This rock volume is minor compared to open pit operations where all overburden layers must be removed to access the ore. As underground mines are developed and ore is removed, common practice involves placing development waste rock into mined-out areas to avoid moving it to the surface and to minimize surface disturbance.
Underground uranium mining has very stringent regulatory requirements for ventilation. The presence of radon gas in uranium mines, resulting from the natural radioactive decay of uranium, dictates that large volumes of air must be moved through mines to reduce the gas concentrations.
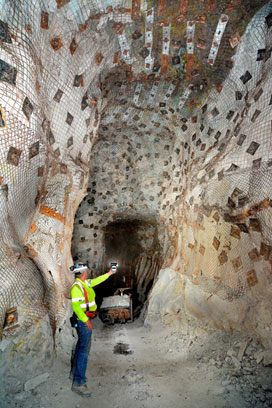
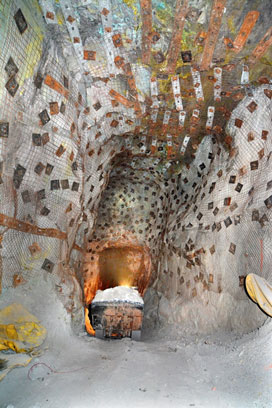
The control of radon in mines is monitored closely to ensure that radon concentrations meet all Mine Safety and Health Administration (“MSHA”) requirements. The legacy of health impacts to uranium miners in the early years of underground uranium mining has led to today’s very tight controls. In historical mining operations, the combination of radon gas, silica dust from the sandstone ore, and cigarette smoking combined to result in abnormally high incidences of lung cancers and related ailments. All of these factors have been eliminated or are strictly regulated (no smoking allowed) in the modern mining environment. All underground mines have extensive ventilation systems, incorporating multiple vertical shafts and fans, to supply fresh air into the mines.
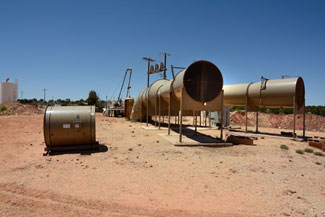
Mining operations are authorized under operating permits issued by state agencies. If mines are on U.S. public domain lands, federal agencies are also extensively involved in the permitting process. A modern mine permit requires that the mine operator provide financial surety to cover all costs required to decommission a mine site, fully reclaim such a site, and return it to its pre-mining beneficial use.
Upon completion of mining operations, mine reclamation is generally straightforward for an underground operation. Following removal of underground equipment and service facilities, all mine openings are permanently sealed (although there have been interesting developments in recent years where mine openings are barricaded, but left accessible to provide excellent “bat habitat” as requested by regulatory agencies). Surface facilities are removed, and the mine site and waste rock dumps can be regraded and reclaimed, with the land surface being returned to its former productive use. Typical underground uranium mine sites range from 10 to 25 acres.
Uranium Ore Milling
After uranium ore is removed from the ground, it must be processed to extract the contained uranium. This process, “milling,” involves a sequence of physical and chemical treatment steps to extract the uranium from the native rock. The final product of milling is yellowcake or U3O8, which is the commercial product sold by uranium producers to nuclear utility customers.
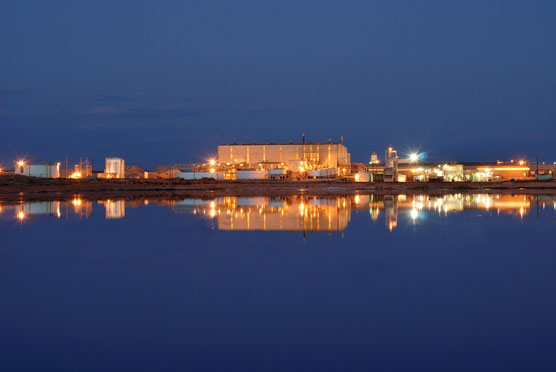
During the peak U.S. uranium production period of the early 1980’s, a total of 26 uranium mills were operating, and the U.S. was the world’s leading uranium producer. Today, there are three uranium mills remaining in the U.S. Two of these are currently authorized for operations and only one is actually operating today.
Uranium milling employs equipment and metallurgical processes, adapted from other extractive industries, specifically tailored to uranium recovery. The uranium mills of past decades and the mills in existence today have capacities ranging from 500 ore tons per day up to 3,000 tons per day. At average historical ore grades, annual uranium concentrate production normally ranged from around 1,000,000 pounds of yellowcake up to more than 7,000,000 pounds of yellowcake for the largest U.S. operations.
Uranium milling starts with the delivery of mined ore to the mill, where the ore is weighed and sampled to determine the uranium content and to prepare samples for process testing. Ore stockpiles are constructed to store sufficient ore volume to run the mill for a continuous period and to provide a “blend” of ore to ensure consistent feed to the mill. The first stage is crushing and grinding where the ore is reduced down to individual grains to ensure that the uranium mineralization is exposed to the leaching agents.
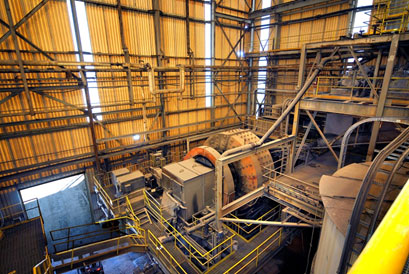
Ore suspended in water, or “pulped” ore, is fed to a multi-stage leaching circuit. Here the pulp is typically heated to enhance chemical reactivity, and leaching is initiated by addition of sulfuric acid or bicarbonate, depending on the basic mill design and ore amenability. The ore passes through several stages of leaching as leach agent and oxidizer concentrations are adjusted to achieve optimum dissolution of uranium (and also vanadium if present in the ore). With most of the uranium in solution, the ore slurry passes to a solid/liquid separation circuit, or CCD circuit, which is a series of large vessels where the slurry is mixed with wash water to remove as much uranium as possible and also separate the uranium-bearing liquor from the leached solids.
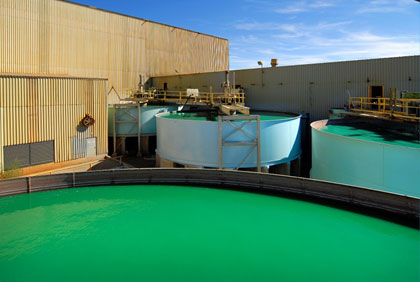
At the completion of the CCD circuit, all recoverable uranium (typically in excess of 98% of the original uranium content) is in solution. The leached solids are pumped to the uranium mill tailings disposal cells which are required to be designed and constructed with layers of impermeable lining material and a sophisticated leak detection system to assure all process chemicals are fully contained.
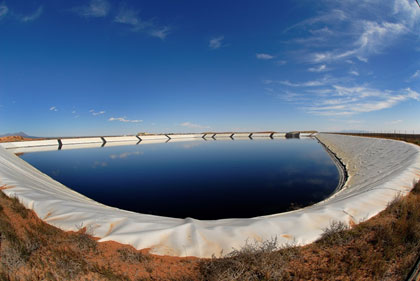
The uranium-bearing liquor proceeds to a solvent extraction (“SX”) or ion exchange (“IX”) circuit. The SX or IX circuit selectively removes uranium from the uranium-bearing aqueous solution; uranium is preferentially collected by the organic solvent in SX or by resin beads in an IX circuit. This stage of uranium processing also concentrates the uranium into a smaller solution volume. The barren aqueous solution can be returned to the processing circuit or disposed in the tailings system.
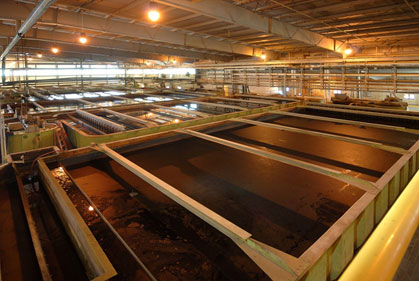
In either SX or IX circuits, the affinity of the selective organic solvent or resin, as the case may be, for uranium is the key stage in removing uranium from a water-based solution. Uranium is stripped from the SX solvent or IX resin by a saline solution. This saline solution is the culmination of several steps to increase the concentration of uranium, and this solution is now ready to yield the final product. Uranium is precipitated from this strip solution by addition of ammonia or peroxide. The precipitated uranium is now a yellow slurry (hence “yellowcake”).
The yellowcake slurry is washed to remove contaminants and dewatered to form a thick paste. Final product preparation involves drying the yellowcake paste to remove free water. Drying is typically conducted in a high temperature furnace which bakes the cake, or it can also be dried in a rotary drum dryer. Yellowcake dryers are typically fired by propane or natural gas.
Dried yellowcake is packaged in steel 55-gallon drums, each containing about 800 to 1,000 pounds. Yellowcake is the final product of uranium mining and milling, and this is the product sold by producers to utility customers. Yellowcake subsequently goes through a number of complex processing steps (conversion, enrichment, fuel fabrication) on its way to becoming fuel for a nuclear power plant.
Regulatory and Environmental
Uranium processing facilities are subject to some of the most stringent environmental and regulatory controls of any industrial complex, and must have full on-site capability to quickly analyze and identify potential problems so that responses can be immediate and effective.
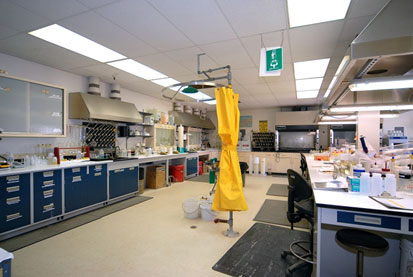
To recover uranium by any process, a Source Material License (or equivalent) is required. Uranium mill licensing and regulatory oversight is normally the purview of the U.S. Nuclear Regulatory Commission. Utah, Colorado, and Texas are “Agreement States” and are in charge of licensing and regulatory oversight; however, the states must meet or exceed the requirements of the Nuclear Regulatory Commission to attain Agreement State status.
Uranium processing mills must be sited in areas that can meet stringent criteria to ensure that uranium mill tailings can be isolated from the environment. All possible contaminant transport pathways are exhaustively studied to ensure mill tailings can be isolated. A uranium mill constructed and operated to current standards must be a zero-discharge facility, meaning that nothing can be allowed to leave the defined perimeter of the facility.
Modern regulations require that uranium mill tailings can only be stored in specially designed and constructed cells, with multiple synthetic and clay liners, to prevent any leakage of spent mill solutions. During operations, mill tailings must be stable and in a strictly controlled area to prevent transport of tailings materials off licensed sites. A plan for final mill decommissioning and closure of the tailings cells, in a manner to ensure isolation of the tailings from the surrounding environment, must be approved by the appropriate regulatory authorities. Prior to the start of milling operations, operators must provide financial surety adequate to fully decommission the mill and reclaim the mill site and tailings cells. This surety is reviewed annually and updated as necessary.
Operators of uranium processing mills are required to own the land on which the mill and tailings facilities are located. Upon completion of milling operations and final closure and reclamation, the reclaimed site is then deeded to the U.S. Department of Energy for perpetual care. Mill operators must fund a perpetual care account prior to starting operations – these funds are in addition to the closure and reclamation surety.
During active operations, uranium recovery facilities adhere to rigorous radiation monitoring and safety programs. These programs cover all workers as well as the surrounding air, soils, vegetation, wildlife, surface water, and ground water systems. These programs include extensive employee indoctrination, employee scans and bioassays, the use of Personal Protective Equipment when required, comprehensive sampling and reporting of all results to appropriate regulatory agencies, external audits and surveys, and direct corporate managerial involvement in all radiation control programs.