Conversion Process
Honeywell Dry Fluoride Volatility Conversion Process
The dry fluoride volatility conversion process developed by Honeywell International delivers a UF6 product with a consistently high 99.99% purity. This unique process is comprised of 5 main stages:
- Sizing
- Reduction
- Hydrofluorination
- Fluorination, and
- Distillation,
as well as auxiliary processes such as waste treatment and sodium removal.
Prior to any yellowcake (uranium ore concentrates) entering the conversion process, samples of each lot are taken through an Auger Sampling System to be analyzed for uranium quality and moisture content.
Once fed into the conversion process, yellowcake is uniformly sized and reacted with hydrogen at a high temperature to form uranium dioxide (the Reduction stage). Next, the uranium dioxide (UO2) is reacted with anhydrous hydrofluoric acid in fluidized bed reactors during Hydrofluorination to yield uranium tetrafluoride (UF4). UF4 is reacted with gaseous fluorine to produce crude gaseous uranium hexafluoride (UF6) in the Fluorination stage, and then enters the final Distillation stage. Here, light fraction gases and impurities are removed to produce a purified liquid UF6. This liquid UF6 is drained into 14-ton cylinders where, after cooling for 5 days, the UF6 crystallizes.
How Are We Different?
The dry fluoride conversion process used at Honeywell-MTW is a fully integrated, continuous process, as compared to the two-step processes of all other Western converters.
MTW’s process takes place in one location, under one roof. All other Western converters use two separate facilities which requires packaging and transport of intermediary products.
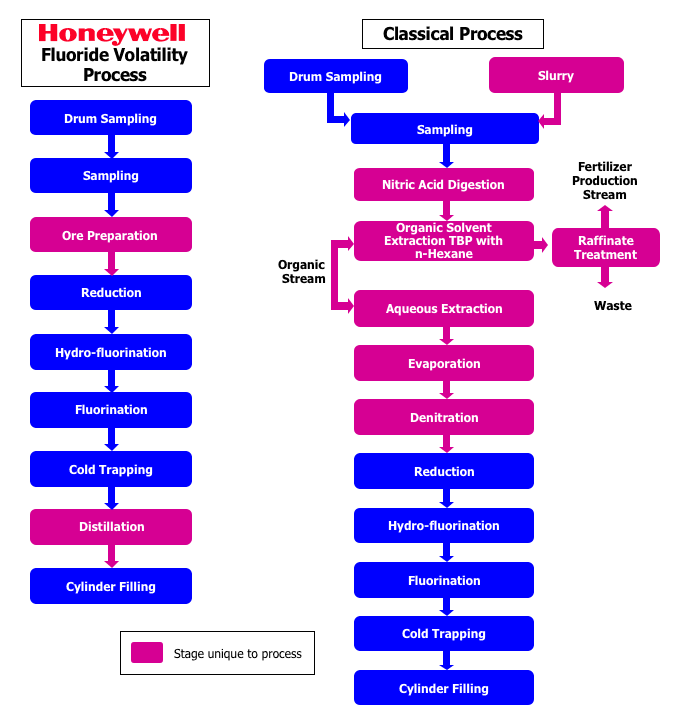